
AutASS: Autonome Antriebstechnik durch Sensorfusion für die intelligente, simulationsbasierte Überwachung & Steuerung von Produktionsanlagen
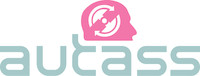
A trend towards more and more complex systems is observable worldwide. Because of the prevailing diversity of topics, solution concepts are often investigated isolated which leads to complexity problems. In the scope of intelligent drive systems for machines or facilities, cognitive approaches can be found many times. Nevertheless, it is noticeable that integral concepts and realisations of such systems for process automation and production technology are still in an early stage or in the state of R&D, respectively, although practicable partly solutions are available in the market. Necessary tools such as algorithmic procedures, sensory systems, development methods, test facilities and production technologies are available in different depths. Nevertheless, application specific toolsets with the necessary adjustments and additions, respectively, to develop and realise industrially applicable drive systems are missing.
The aim of this project is to integrate sensor functionality in electrical drives for creating intelligent, autonomous self-diagnostic capabilities of single components of the drive system and the process and therefore the realisation of mechatronic control circuits. The “health status” (wear and tear, life cycle prognosis) of electrical drives including subsequent processes is determined in good time and reliable by evaluating test signals with the help of combining flexible, modular sensory functions. All sensory units are wirelessly connected with the “intelligent electronics” of the drive. The algorithms applied in there ensure the autonomous function of the “intelligent electronics” by signal analysis capabilities. For executing evaluations as well as providing monitoring control and presenting results, the connected diagnosis center (trend analysis, threshold value definitions, damage prognoses, etc.) is available.
This project belongs to the research scope “Internet of Things” and is funded by the initiative Autonomic Systems of the Federal Ministry of Economics and Technology.

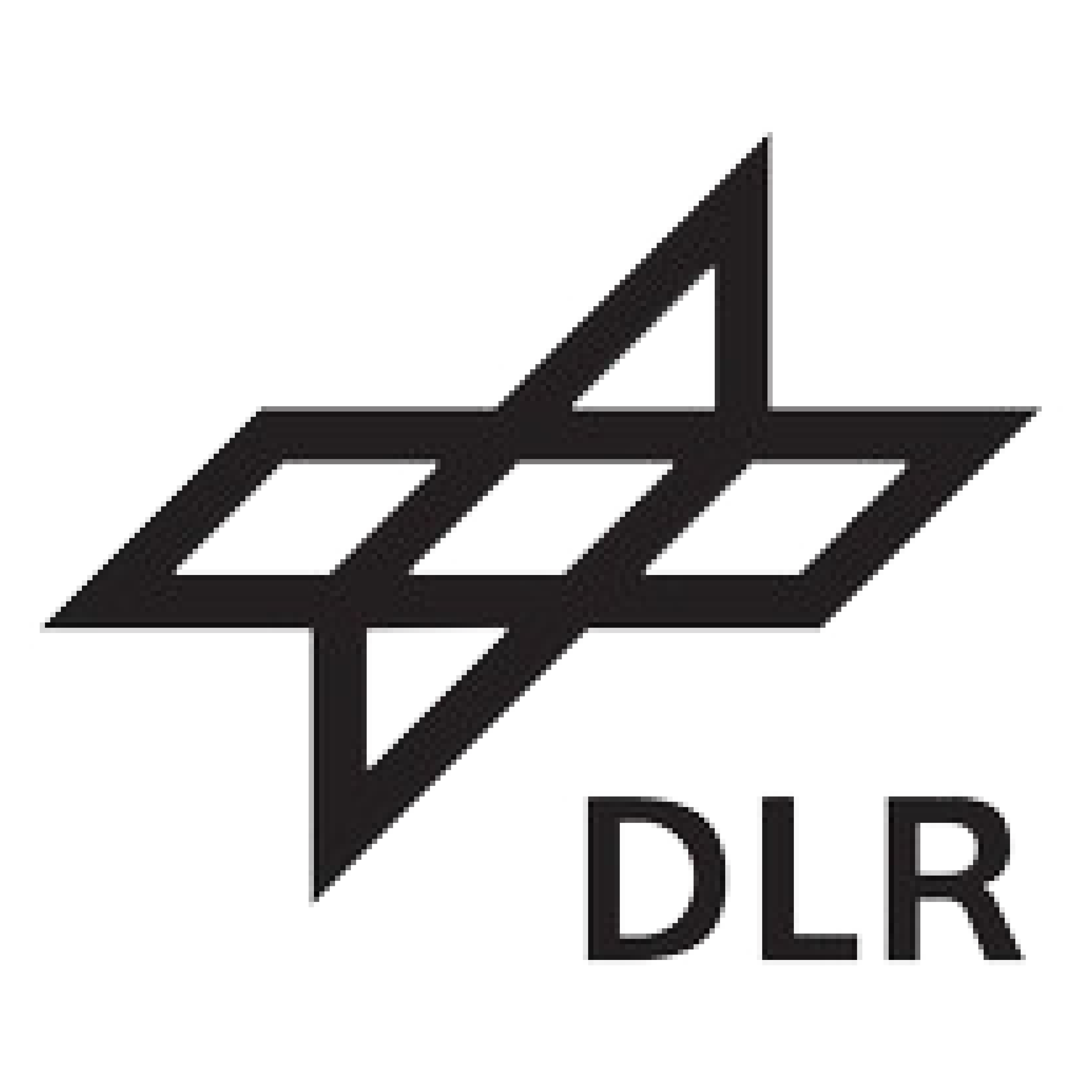